印制电路板废水处理及回用工艺


印制电路板废水依据废水特征可分为含氰废水、含镍废水、高浓度有机废水、低浓度有机废水、络合铜废水、铜氨废水、含铜废水、电镀废水、一般酸碱废水、磨板废水等,各类废水产生的工序详见表1。

1. 含铜废水的处理
1)中和混凝时设定控制pH值应根据现场调试确定,设计可按pH 8 ~ 9进行药剂消耗计算。
2)反应时间宜为 10 ~15 min;
3)铜可降至 0.5 mg/L 以下,出水可作为回用水源或进入综合废水处理系统。
2. 络合铜废水的处理
络合铜废水预处理宜采用化学沉淀法。
1)Fe3+可掩蔽EDTA,从而释放Cu2+;其处理成本廉价,应优先采用;
2)硫化物法可有效去除EDTA-Cu,过量的S可采用Fe盐去除;
3)Fenton氧化可破坏络合剂的部分结构而改变络合性能;
4)重金属捕集剂是螯合剂,能形成更稳定的铜螯合物并且是难溶物;
5)离子交换法可交换离子态的螯合铜,并将其去除。
6)生化处理可改变络合剂或螯合剂性能,释放Cu2+ ,具有广泛的适用性。
铁盐屏蔽法破络阶段 pH 值控制在 2~4,化学氧化和硫化物沉淀法 pH 值宜根据试验确定,沉淀阶段 pH 值宜控制在 8~9;铁盐屏蔽法和硫化物沉淀法可将络合铜废水中总铜处理至 0.5 mg/L 以下,出水进入综合废水处理系统。具体设计应根据试验结果确定破络工艺。
三价盐可掩蔽主要的络合物EDTA;辅助破络反应可采用硫化钠,按沉淀出水Cu<2.0mg/L投加量控制;
生化处理应便于排泥,以排出生化处理破络后形成的铜沉淀物。
如络合铜废水在常规破络后可达到排放要求,则不需进入生化系统处理。
如果没有破坏或者掩蔽络合剂,络合铜废水处理后宜单独排至出水计量槽,以免形成新的络合铜。
3. 铜氨废水的处理
铜氨废水预处理可采用折点加氯法、选择性离子交换法或磷酸铵镁脱氨氮法。
3.1 折点加氯法
铜氨废水的废水水量、氨氮浓度随时间变化不大时,可采用折点加氯法。
2)氧化反应阶段 pH 值宜控制在 4~7 左右,氧化剂宜采用 NaClO,反应时间宜为 30 ~60min;
3)有效氯投加量宜根据试验确定,无试验数据时可按氨氮与氯质量比为 1:(7~10)投加;
4)混凝阶段 pH 值宜控制在 8~9;
5)折点加氯法对废水中氨氮的去除率在 80%以上,出水进入综合废水处理系统。
3.2 磷酸铵镁脱氨氮法
铜氨废水有多种金属离子或有机物时,宜采用磷酸铵镁脱氨氮法。

1)采用碱性氯化法处理含氰废水的氧化剂可采用:次氯酸钠、漂白粉、漂粉精、二氧化氯、或液氯。理论有效氯投加量:CN:NaClO=1:7.16。实际由于废水中还有其它还原物或有机物会消耗有效氯,投药量宜通过试验确定。
2)反应 pH 值条件:一级破氰控制 pH 值 10 ~ 11,反应时间宜为 30 ~ 60 分钟;二级破氰控制 pH值 6.5 ~ 7,反应时间宜为 30 ~ 60 分钟。
3)自动控制 ORP 参考值:一级破氰约 +200 ~ +300 mV,二级破氰约 +600 ~ +650 mV。由于废水中所有还原性物质都可能与氧化剂发生反应,因此对于实际 ORP 控制值,应根据 CN 的剩余浓度现场试验确定。设定 ORP 值的原则是既保证残余 CN 浓度小于排放要求,又不浪费氧化剂。
4)反应池宜采用机械搅拌,机械搅拌速度梯度宜按 500 s -1 ~1000 s -1 设计;反应池宜设置排空管,接入调节池或事故池。
4.2 双氧水法
1)反应池 pH 值应控制在 9~11;
2)双氧水投加量宜按氰离子与双氧水的质量比计算确定,质量比通常取 1 : 5;
3)要求游离氰根设计去除率大于 97%时,接触时间不宜少于 15 min;要求游离氰根设计去除率大于 99%时,接触时间不宜少于 20 min。
5. 有机废水的处理
5.1 高浓度有机废水
高浓有机废水中最大量的是各种油墨产生的浓液,如黑油、干膜、湿膜、绿油等,用于PCB生产过程的图纸像转移抗蚀剂和阻焊抗蚀剂,在有机废水中,黑油呈黑色,干膜/湿膜呈蓝色,绿油呈绿色。因此,经常也有用“油墨废水”、“显影废水”、“菲林废水”来代指高浓有机废水的。其它高浓有机废水(液)如高锰酸钾换缸液及缸后水洗水、膨松剂缸及缸后水洗水、除油剂缸液、清洁剂缸注、网房洗网液、丝印房产生的废液、返洗房洗板液等。高浓度有机废水可在酸性条件下析出固体,再通过固液分离可去除大部分有机物和部分重金属。
1)脱膜、显影废液应首先采用酸析处理。酸析反应控制 pH 值 3 ~ 5,具体数值可现场调整确定。设定的原则是去除率提高平缓时,不再下调 pH 值。酸性条件使得膜的水溶液形成胶体状不溶物,通过固液分离去除;
2)酸析反应宜采用机械搅拌,搅拌机转速宜 100 ~300 rpm;
3)可在酸析池中投加用于减少酸析后固体结块堵塞的改良剂,常用改良剂有粉末活性炭,聚合氯化铝铁等,投加量宜根据试验确定;
4) 酸析后的高浓度有机废水可采用生化处理,也可根据情况采用化学氧化处理;
5)好氧处理须注意控制进水浓度Cu < 5.0mg/L,可以将破络后的络合废水进入好氧池一同处理,通过排泥量控制混合液中的Cu < 20mg/L;
6)高浓度有机废水厌氧处理水力停留时间(HRT)宜 24h 以上,投配负荷:2.0 ~ 3.0 kg COD/ m3.d 以下;
7)高浓度有机废水预处理工艺对有机物去除率可达 80%以上,出水进入低浓度有机废水。
1)采用芬顿氧化去除有机物时,pH 值宜控制在 2~4,芬顿试剂投加量宜根据试验确定,无试验数据时可按 CODCr 与芬顿试剂质量比 1:(1~3)投加,反应时间 1~2 h;为减少残留的 H2O2对后续沉淀影响,可在芬顿氧化后投加还原剂;
2)采用铁-碳微电解去除有机物时,pH 值宜控制在 3~5,空气搅拌气量不小于 3 ~5 m3 /m2 .h,填料接触时间不小于 30 min;填料在反应池中应分层堆放,每层单独设置空气搅拌系统;
3)混凝阶段 pH 值宜为 8~9,反应时间宜为 10 ~15 min;
4)低浓度有机废水经过预处理后有机物去除率可达 50~80%,铜可降至 1 mg/L以下,出水进入综合废水处理系统。
6. 含镍废水的处理
印制电路板废水中的含镍废水来源化学度金、板面电镀金、金手指和各相对应生产线的退镀液工序的废缸液和缸后水洗水。镍是属于废水中的第一类污染物,含镍污泥归类为危险废弃物,污泥的处置受到严格限止,要单独分开处理,同时也是较贵重金属,废水中的镍具有回收价值。根据环保法规要求,含镍废水须单独分开处理。含镍废水可采用化学沉淀法、离子交换法或反渗透法。
6.1 化学沉淀法
含镍废水混有其它金属类污染物和有机污染物时,应采用化学沉淀法。
6)含镍废水中仅含离子态镍时可不设置破络工艺;
7)含镍废水经化学沉淀将镍处理达标后,可作为回用水源或进入综合废水处理系统。
6.2 离子交换法
含镍废水污染物成分较单一、主要以离子态镍为主,或者要求回收镍时,可采用离子交换法。
1)进水镍离子浓度不宜大于 200 mg/L;
2)阳离子树脂宜采用钠型凝胶型强酸阳离子交换树脂、大孔型弱酸阳离子交换树脂、凝胶型弱酸阳离子交换树脂或选择性强的特种树脂;
3)设计、运行控制技术条件和参数,应符合 GB 50136 的规定;
4)含镍废水经离子交换将镍处理达标后,可作为回用水源或进入综合废水处理系统;
5)交换再生液可回收或按危险废物处置。
6.3 反渗透法
含镍废水要求车间在线回收时,可采用反渗透法。
1)进水硬度不宜大于 100 mg/L(CaCO3 ),当硬度大于 500 mg/L(CaCO3 )时,宜采用氢氧化钠和碳酸钠软化处理;当硬度小于 500 mg/L(CaCO3 )时,宜投加阻垢剂。药剂具体投加量应通过试验确定;
2)进水余氯应小于 1.0 mg/L,当余氯大于 1.0 mg/L 时,宜投加还原剂处理;
3)反渗透处理设备的设计使用应参照膜厂家提供的技术资料和 GB/T 19249;
4)反渗透产水直接回用于生产线;浓水可采用化学沉淀法处理或回镀槽。
7. 综合废水的处理
7.1 经预处理后的综合废水pH值应控制在 7~9,宜采用生化处理工艺。生化处理进水有害物质浓度控制应参考 GB50014。综合废水生化处理工艺包括厌氧、缺氧和好氧单元,相关设计要求可参考HJ 576、HJ 2010、HJ 2014、HJ 2009等。
7.2 厌氧单元
1)厌氧池设计参数应通过试验或参照类似工程确定,无详细资料时停留时间宜按 8~16 h 考虑;
2)厌氧池排泥周期和排泥量应综合考虑重金属富集浓度和除磷效果。
7.3 缺氧单元
缺氧池底部应设置潜水搅拌机,防止污泥沉降。
7.4 好氧单元
1)好氧池设计参数应通过试验或参照类似工程确定,无详细资料时停留时间宜按 8~12h 考虑;
2)好氧单元宜采用活性污泥法,方便检修及排泥,防止重金属富集;
3)环境敏感、脆弱的特殊地区执行较为严格的排放标准时,宜选用 MBR 膜生物反应器。
二、废水回用
2. 电镀废水回用
电镀废水包含了图形电镀和板面电镀线产生的水洗水,该水量占总水量约15-20%,水质较好,不含络合物,重金属主要含Cu2+,有机物含量低,一般COD在50 mg/L以下,可处理后回用。
3. 一般酸碱废水回用
磨板废水和电镀废水回用只能达到总水量的40%左右,当政策强制要求印制电路板废水回用率达50%(清洁生产一级要求废水回用率>55%)以上时,只能再将一部分酸碱水洗水深度处理后回用。一般酸碱废水指除去磨板废水、电镀废水、含络合物水洗水,含较高有机物的水洗水之外其它一切生产线水洗水。来自于绝大部分生产线,一般含较少量的络合物、有机物,重金属主要含铜和微量的镍、锡等。
适当的低回用率要求,在技术上并不难,投资上也不是很高,印制电路板企业易接受。但当印制电路板废水的循环回用率要求达50%上,有的要求回用率达85%,更有要求零排放的案例。这在技术上仍有不少难度,第一,很高回用率的要求,回用水对印制电路板产品而言存在较大风险,企业不易接受;第二,投资较大,运行成本也较高,企来不愿接受。
回用水处理工艺宜采用过滤+双膜(超滤膜和反渗透膜)组合工艺,膜处理工艺设计应符合 HJ 579 的规定;成分单一、电导率较低的废水可采用离子交换工艺。
表1 印制电路板废水水质水量分类表 (单位:mg/L,pH 除外)

含金、银等贵金属废水应线上回收,一般不纳入废水治理工程。
一、废水处理1. 含铜废水的处理

图1 含铜废水的化学法处理流程
1)中和混凝时设定控制pH值应根据现场调试确定,设计可按pH 8 ~ 9进行药剂消耗计算。
2)反应时间宜为 10 ~15 min;
3)铜可降至 0.5 mg/L 以下,出水可作为回用水源或进入综合废水处理系统。
2. 络合铜废水的处理
络合铜废水预处理宜采用化学沉淀法。

图2 络合铜的基本处理流程
常用破络剂有铁盐、硫化物、芬顿试剂、重捕剂,常用破络方法有铁盐屏蔽法、硫化物沉淀法、化学氧化法(芬顿试剂)等。1)Fe3+可掩蔽EDTA,从而释放Cu2+;其处理成本廉价,应优先采用;
2)硫化物法可有效去除EDTA-Cu,过量的S可采用Fe盐去除;
3)Fenton氧化可破坏络合剂的部分结构而改变络合性能;
4)重金属捕集剂是螯合剂,能形成更稳定的铜螯合物并且是难溶物;
5)离子交换法可交换离子态的螯合铜,并将其去除。
6)生化处理可改变络合剂或螯合剂性能,释放Cu2+ ,具有广泛的适用性。
铁盐屏蔽法破络阶段 pH 值控制在 2~4,化学氧化和硫化物沉淀法 pH 值宜根据试验确定,沉淀阶段 pH 值宜控制在 8~9;铁盐屏蔽法和硫化物沉淀法可将络合铜废水中总铜处理至 0.5 mg/L 以下,出水进入综合废水处理系统。具体设计应根据试验结果确定破络工艺。
三价盐可掩蔽主要的络合物EDTA;辅助破络反应可采用硫化钠,按沉淀出水Cu<2.0mg/L投加量控制;
生化处理应便于排泥,以排出生化处理破络后形成的铜沉淀物。
如络合铜废水在常规破络后可达到排放要求,则不需进入生化系统处理。
如果没有破坏或者掩蔽络合剂,络合铜废水处理后宜单独排至出水计量槽,以免形成新的络合铜。
3. 铜氨废水的处理
铜氨废水预处理可采用折点加氯法、选择性离子交换法或磷酸铵镁脱氨氮法。
3.1 折点加氯法
铜氨废水的废水水量、氨氮浓度随时间变化不大时,可采用折点加氯法。

图3 铜氨废水折点加氯法的预处理工艺流程
1)进水氨氮浓度不宜大于 50 mg/L;2)氧化反应阶段 pH 值宜控制在 4~7 左右,氧化剂宜采用 NaClO,反应时间宜为 30 ~60min;
3)有效氯投加量宜根据试验确定,无试验数据时可按氨氮与氯质量比为 1:(7~10)投加;
4)混凝阶段 pH 值宜控制在 8~9;
5)折点加氯法对废水中氨氮的去除率在 80%以上,出水进入综合废水处理系统。
3.2 磷酸铵镁脱氨氮法
铜氨废水有多种金属离子或有机物时,宜采用磷酸铵镁脱氨氮法。

图4 铜氨废水磷酸铵镁脱氨氮法的预处理工艺流程
1)反应池 pH 值宜控制在 9.5~10.5;
2)反应时间宜大于 30 min;
3)镁盐宜采用 MgCl2 . 6H2O 或 MgSO4 . 7H2O,磷酸盐宜采用 Na2HPO4 . 12H2O;
4)N:P:Mg 对氨氮处理效果影响较大,应通过试验确定,无试验数据时可按 NH4+ 、PO43- 、Mg2+ 摩尔比为 1:1.2:1.3 投加;
5)磷酸铵镁脱氨氮法对废水中氨氮的去除率在 80%以上,出水进入综合废水处理系统;
4. 含氰废水的处理
印制电路板生产线含氰化物的单元有板面电镀金、金手指、退镀液、化学度金、化学镀镍、化学镀铜(沉铜缸),缸后水洗为含氰废水。含氰废水应避免铁、镍离子混入,含氰废水的预处理可采用碱性氯化法和双氧水氧化法两种工艺。破氰后的废水应再进行重金属的去除。
4.1 碱性氯化法
2)反应时间宜大于 30 min;
3)镁盐宜采用 MgCl2 . 6H2O 或 MgSO4 . 7H2O,磷酸盐宜采用 Na2HPO4 . 12H2O;
4)N:P:Mg 对氨氮处理效果影响较大,应通过试验确定,无试验数据时可按 NH4+ 、PO43- 、Mg2+ 摩尔比为 1:1.2:1.3 投加;
5)磷酸铵镁脱氨氮法对废水中氨氮的去除率在 80%以上,出水进入综合废水处理系统;
6)使用中应考虑采取预防管道结垢、堵塞措施。
4. 含氰废水的处理
印制电路板生产线含氰化物的单元有板面电镀金、金手指、退镀液、化学度金、化学镀镍、化学镀铜(沉铜缸),缸后水洗为含氰废水。含氰废水应避免铁、镍离子混入,含氰废水的预处理可采用碱性氯化法和双氧水氧化法两种工艺。破氰后的废水应再进行重金属的去除。
4.1 碱性氯化法

图5 含氰废水碱性氯化法预处理基本处理流程
1)采用碱性氯化法处理含氰废水的氧化剂可采用:次氯酸钠、漂白粉、漂粉精、二氧化氯、或液氯。理论有效氯投加量:CN:NaClO=1:7.16。实际由于废水中还有其它还原物或有机物会消耗有效氯,投药量宜通过试验确定。
2)反应 pH 值条件:一级破氰控制 pH 值 10 ~ 11,反应时间宜为 30 ~ 60 分钟;二级破氰控制 pH值 6.5 ~ 7,反应时间宜为 30 ~ 60 分钟。
3)自动控制 ORP 参考值:一级破氰约 +200 ~ +300 mV,二级破氰约 +600 ~ +650 mV。由于废水中所有还原性物质都可能与氧化剂发生反应,因此对于实际 ORP 控制值,应根据 CN 的剩余浓度现场试验确定。设定 ORP 值的原则是既保证残余 CN 浓度小于排放要求,又不浪费氧化剂。
4)反应池宜采用机械搅拌,机械搅拌速度梯度宜按 500 s -1 ~1000 s -1 设计;反应池宜设置排空管,接入调节池或事故池。
4.2 双氧水法

图6 含氰废水双氧水法预处理基本处理流程
1)反应池 pH 值应控制在 9~11;
2)双氧水投加量宜按氰离子与双氧水的质量比计算确定,质量比通常取 1 : 5;
3)要求游离氰根设计去除率大于 97%时,接触时间不宜少于 15 min;要求游离氰根设计去除率大于 99%时,接触时间不宜少于 20 min。
5. 有机废水的处理
5.1 高浓度有机废水
高浓有机废水中最大量的是各种油墨产生的浓液,如黑油、干膜、湿膜、绿油等,用于PCB生产过程的图纸像转移抗蚀剂和阻焊抗蚀剂,在有机废水中,黑油呈黑色,干膜/湿膜呈蓝色,绿油呈绿色。因此,经常也有用“油墨废水”、“显影废水”、“菲林废水”来代指高浓有机废水的。其它高浓有机废水(液)如高锰酸钾换缸液及缸后水洗水、膨松剂缸及缸后水洗水、除油剂缸液、清洁剂缸注、网房洗网液、丝印房产生的废液、返洗房洗板液等。高浓度有机废水可在酸性条件下析出固体,再通过固液分离可去除大部分有机物和部分重金属。
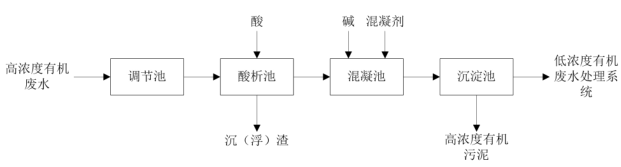
图7 高浓度有机废水预处理基本处理流程
1)脱膜、显影废液应首先采用酸析处理。酸析反应控制 pH 值 3 ~ 5,具体数值可现场调整确定。设定的原则是去除率提高平缓时,不再下调 pH 值。酸性条件使得膜的水溶液形成胶体状不溶物,通过固液分离去除;
2)酸析反应宜采用机械搅拌,搅拌机转速宜 100 ~300 rpm;
3)可在酸析池中投加用于减少酸析后固体结块堵塞的改良剂,常用改良剂有粉末活性炭,聚合氯化铝铁等,投加量宜根据试验确定;
4) 酸析后的高浓度有机废水可采用生化处理,也可根据情况采用化学氧化处理;
5)好氧处理须注意控制进水浓度Cu < 5.0mg/L,可以将破络后的络合废水进入好氧池一同处理,通过排泥量控制混合液中的Cu < 20mg/L;
6)高浓度有机废水厌氧处理水力停留时间(HRT)宜 24h 以上,投配负荷:2.0 ~ 3.0 kg COD/ m3.d 以下;
7)高浓度有机废水预处理工艺对有机物去除率可达 80%以上,出水进入低浓度有机废水。
5.2 低浓度有机废水
低浓度有机废水是某些较高有机物浓度的缸后水洗水,如显影缸后水洗水、退膜缸后水洗水、酸性,碱性除油缸后水洗水等。低浓度有机废水预处理可采用化学氧化法或铁-碳微电解法去除有机物,采用化学沉淀法去除重金属。
低浓度有机废水是某些较高有机物浓度的缸后水洗水,如显影缸后水洗水、退膜缸后水洗水、酸性,碱性除油缸后水洗水等。低浓度有机废水预处理可采用化学氧化法或铁-碳微电解法去除有机物,采用化学沉淀法去除重金属。

图8 低浓度有机废水预处理基本处理流程
1)采用芬顿氧化去除有机物时,pH 值宜控制在 2~4,芬顿试剂投加量宜根据试验确定,无试验数据时可按 CODCr 与芬顿试剂质量比 1:(1~3)投加,反应时间 1~2 h;为减少残留的 H2O2对后续沉淀影响,可在芬顿氧化后投加还原剂;
2)采用铁-碳微电解去除有机物时,pH 值宜控制在 3~5,空气搅拌气量不小于 3 ~5 m3 /m2 .h,填料接触时间不小于 30 min;填料在反应池中应分层堆放,每层单独设置空气搅拌系统;
3)混凝阶段 pH 值宜为 8~9,反应时间宜为 10 ~15 min;
4)低浓度有机废水经过预处理后有机物去除率可达 50~80%,铜可降至 1 mg/L以下,出水进入综合废水处理系统。
6. 含镍废水的处理
印制电路板废水中的含镍废水来源化学度金、板面电镀金、金手指和各相对应生产线的退镀液工序的废缸液和缸后水洗水。镍是属于废水中的第一类污染物,含镍污泥归类为危险废弃物,污泥的处置受到严格限止,要单独分开处理,同时也是较贵重金属,废水中的镍具有回收价值。根据环保法规要求,含镍废水须单独分开处理。含镍废水可采用化学沉淀法、离子交换法或反渗透法。
6.1 化学沉淀法
含镍废水混有其它金属类污染物和有机污染物时,应采用化学沉淀法。

图9 含镍废水化学沉淀法预处理基本处理流程
1)pH 调节池 1 的 pH 值应控制在 2~3;
2)破络剂可选择芬顿试剂或次氯酸钠,反应时间宜大于 60 min,宜采用机械搅拌;
3)pH 调节池 2 的 pH 值应控制在 10~11;
4)混凝反应宜采用机械搅拌方式,平均速度梯度宜为 30 s -1 ~60 s -1 ,混凝时间宜为10~30 min;
5)沉淀池的设计参数应根据废水处理试验数据或参照类似废水处理的沉淀池运行数据确定;当没有试验条件和缺乏有关资料时,设计参数可参考表 2确定;
2)破络剂可选择芬顿试剂或次氯酸钠,反应时间宜大于 60 min,宜采用机械搅拌;
3)pH 调节池 2 的 pH 值应控制在 10~11;
4)混凝反应宜采用机械搅拌方式,平均速度梯度宜为 30 s -1 ~60 s -1 ,混凝时间宜为10~30 min;
5)沉淀池的设计参数应根据废水处理试验数据或参照类似废水处理的沉淀池运行数据确定;当没有试验条件和缺乏有关资料时,设计参数可参考表 2确定;
表2 沉淀池设计参数表

6)含镍废水中仅含离子态镍时可不设置破络工艺;
7)含镍废水经化学沉淀将镍处理达标后,可作为回用水源或进入综合废水处理系统。
6.2 离子交换法
含镍废水污染物成分较单一、主要以离子态镍为主,或者要求回收镍时,可采用离子交换法。

图10 含镍废水离子交换法预处理基本处理流程
1)进水镍离子浓度不宜大于 200 mg/L;
2)阳离子树脂宜采用钠型凝胶型强酸阳离子交换树脂、大孔型弱酸阳离子交换树脂、凝胶型弱酸阳离子交换树脂或选择性强的特种树脂;
3)设计、运行控制技术条件和参数,应符合 GB 50136 的规定;
4)含镍废水经离子交换将镍处理达标后,可作为回用水源或进入综合废水处理系统;
5)交换再生液可回收或按危险废物处置。
6.3 反渗透法
含镍废水要求车间在线回收时,可采用反渗透法。

图11 含镍废水反渗透法预处理基本处理流程
1)进水硬度不宜大于 100 mg/L(CaCO3 ),当硬度大于 500 mg/L(CaCO3 )时,宜采用氢氧化钠和碳酸钠软化处理;当硬度小于 500 mg/L(CaCO3 )时,宜投加阻垢剂。药剂具体投加量应通过试验确定;
2)进水余氯应小于 1.0 mg/L,当余氯大于 1.0 mg/L 时,宜投加还原剂处理;
3)反渗透处理设备的设计使用应参照膜厂家提供的技术资料和 GB/T 19249;
4)反渗透产水直接回用于生产线;浓水可采用化学沉淀法处理或回镀槽。
7. 综合废水的处理
7.1 经预处理后的综合废水pH值应控制在 7~9,宜采用生化处理工艺。生化处理进水有害物质浓度控制应参考 GB50014。综合废水生化处理工艺包括厌氧、缺氧和好氧单元,相关设计要求可参考HJ 576、HJ 2010、HJ 2014、HJ 2009等。
7.2 厌氧单元
1)厌氧池设计参数应通过试验或参照类似工程确定,无详细资料时停留时间宜按 8~16 h 考虑;
2)厌氧池排泥周期和排泥量应综合考虑重金属富集浓度和除磷效果。
7.3 缺氧单元
缺氧池底部应设置潜水搅拌机,防止污泥沉降。
7.4 好氧单元
1)好氧池设计参数应通过试验或参照类似工程确定,无详细资料时停留时间宜按 8~12h 考虑;
2)好氧单元宜采用活性污泥法,方便检修及排泥,防止重金属富集;
3)环境敏感、脆弱的特殊地区执行较为严格的排放标准时,宜选用 MBR 膜生物反应器。
二、废水回用
当PCB废水要求回用且要达到一定的回用率的情况下,首先要根据生产线的用水水质要求和排水水质特点,选择合适的处理工艺,既能满足回有水质要求和回用率(回用率是强制标准),还要确保余下的捧放水达标排放、降低工程投资和运行成本。应优先采用清洁废水作为回用水水源,含高有机物、络合物清洗水不宜作为回用水源,根据印制电路板废水特点,较易实现废水回用的种类主要有磨板废水、电镀废水、一般酸碱废水,三者中磨板废水回用难度较低、一般酸碱废水回用难度相对较高。当设计废水回用系统时,需核算废水回用后反渗透浓水对总排水的影响,并依此调整废水整体处理工艺。
1. 磨板废水回用
磨板一般采用火山灰磨板或毡辘磨板,磨板废水来自机械磨板机和刷光机酸洗后水洗废水,磨板废水成分简单,除含有大量的机械性磨料及铜粉外,还含有很少量的溶解性Cu2+,过程基本不增加有机物,不含NH3-N、Ni等污染物。印制电路板的废水循环回用,可首先考虑磨板废水回用处理,该水量占总水量约15 ~ 25%。有些企业,直接在车间磨扳线旁安装铜粉过滤机,有些企业则收集后再处理。
1. 磨板废水回用
磨板一般采用火山灰磨板或毡辘磨板,磨板废水来自机械磨板机和刷光机酸洗后水洗废水,磨板废水成分简单,除含有大量的机械性磨料及铜粉外,还含有很少量的溶解性Cu2+,过程基本不增加有机物,不含NH3-N、Ni等污染物。印制电路板的废水循环回用,可首先考虑磨板废水回用处理,该水量占总水量约15 ~ 25%。有些企业,直接在车间磨扳线旁安装铜粉过滤机,有些企业则收集后再处理。

图12 火山灰磨板废水回用基本处理流程

图13 毡辘磨板废水回用基本处理流程
2. 电镀废水回用
电镀废水包含了图形电镀和板面电镀线产生的水洗水,该水量占总水量约15-20%,水质较好,不含络合物,重金属主要含Cu2+,有机物含量低,一般COD在50 mg/L以下,可处理后回用。

图14 电镀废水回用基本处理流程
3. 一般酸碱废水回用
磨板废水和电镀废水回用只能达到总水量的40%左右,当政策强制要求印制电路板废水回用率达50%(清洁生产一级要求废水回用率>55%)以上时,只能再将一部分酸碱水洗水深度处理后回用。一般酸碱废水指除去磨板废水、电镀废水、含络合物水洗水,含较高有机物的水洗水之外其它一切生产线水洗水。来自于绝大部分生产线,一般含较少量的络合物、有机物,重金属主要含铜和微量的镍、锡等。
适当的低回用率要求,在技术上并不难,投资上也不是很高,印制电路板企业易接受。但当印制电路板废水的循环回用率要求达50%上,有的要求回用率达85%,更有要求零排放的案例。这在技术上仍有不少难度,第一,很高回用率的要求,回用水对印制电路板产品而言存在较大风险,企业不易接受;第二,投资较大,运行成本也较高,企来不愿接受。
回用水处理工艺宜采用过滤+双膜(超滤膜和反渗透膜)组合工艺,膜处理工艺设计应符合 HJ 579 的规定;成分单一、电导率较低的废水可采用离子交换工艺。

图15 一般酸碱废水回用基本处理流程
超滤浓水可进入低浓度有机废水处理系统进行处理,亦可单独收集处理。

图16 超滤浓水处理流程
反渗透浓水可进入预处理系统或单独处理,进入预处理系统处理时应确保不会引起盐分积累。

图17 反渗透浓水处理流程
上一篇 : 电镀废水稳定达标排放的影响因素及对策
下一篇 : 反渗透膜在废水零排放中有什么应用限制?